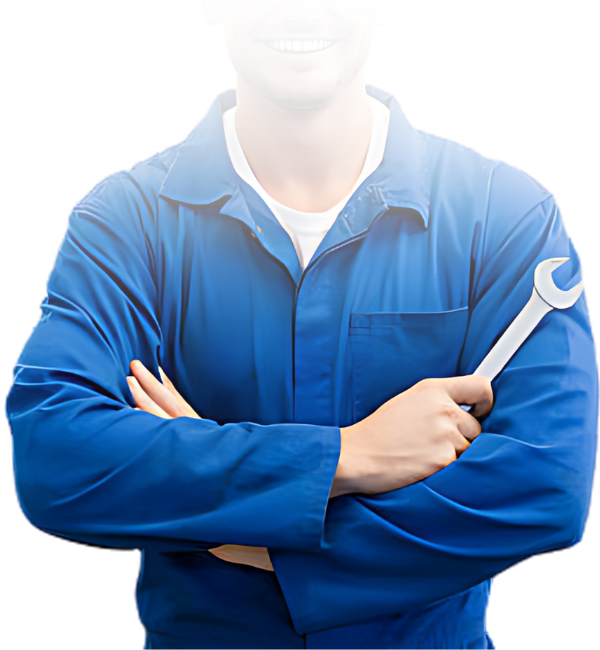
Our process
Reconditioning Process:
Step 1 : Component Stripping
A professional engineer strips the unit fully down to the bolts while analysing and updating logs on potential faults/damage recording parts gathered and its location.


Step 2 : Thorough Chemical Clean/Decoke
We use industry grade chemicals, equipment and pressure washers to purge the component of carbon, foreign contaminants and lubricants. This results in a component that is as free of obstacles to functionality as possible, we dry our components with pressurised air to avoid rust and allow for further inspections and tests to be carried out without obstruction or false results
Step 3 : Testing and Supply
We go through rigorous testing of components with various use of equipment measuring tools and gauges, then if machining is required, we proceed with our in-house machinists who skillfully operate on it till it passes our quality checks. The parts team will subsequently check our stock or supply parts needed from our suppliers at the best price at a high quality.
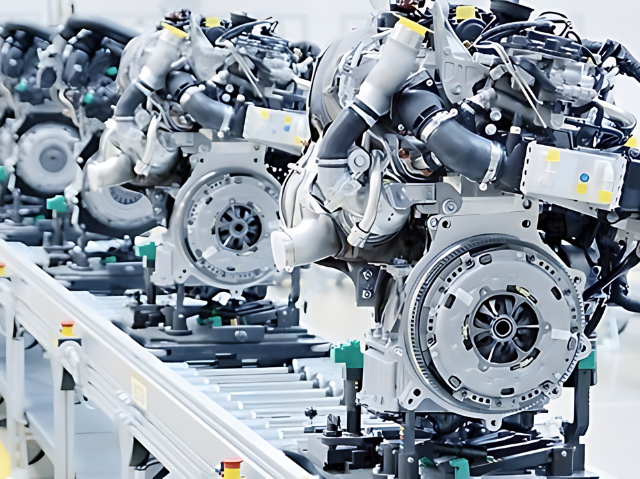
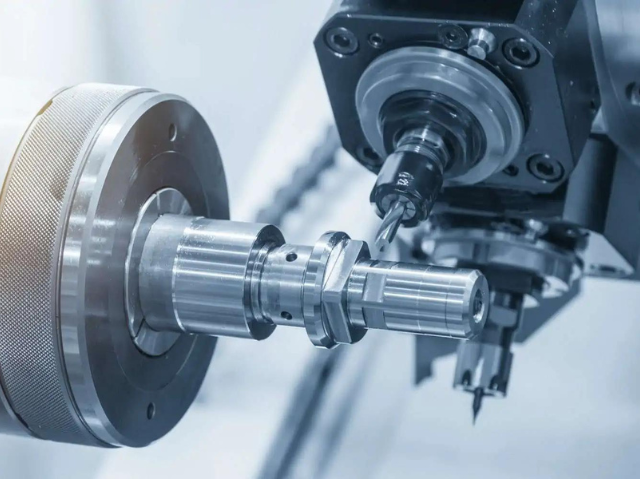
Step 4 : Precision Machining
Cylinder heads are checked for broken bolts, cracks, loose guides and damaged seats etc., they are pressure tested to ensure no head has unseen damage and can be reconditioned, it is then vac tested and valves are checked, lapped and seats are changed and ground if required.
Camshafts are wire wheeled and polished. Clearance is adjusted to industry standards and if the head has buckets/shims they are adjusted to meet stringent standards. Heads are surface ground and sprayed then rebuilt.
Crankshaft is ground if required and are always polished and new bearings are used, crankshaft straightness is checked and adjusted if required.
Blocks are surface ground and bored, honed and sleeved if needed.
Step 5 : Rebuild
Engine components are rebuilt with quality lubricants and engines come with new bearings, seals, gaskets and bolts which are torqued precisely according to industry data using advanced software.
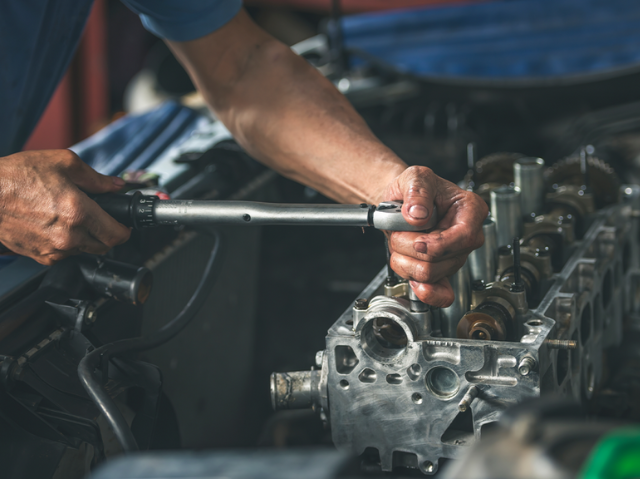

Step 6 : Quality Control
Quality is a top priority for us at Eurojap and we inspect and monitor work at each step to maximise it. A second opinion is used to cross-reference work, manage errors and make sure it does not reach the customer at a substandard level. The warranties are placed on our engines once it has passed the quality checks.
Step 7 : Fitting or Dispatch
Engine will be dispatched once payment is received and customer will be sent an invoice and warranty forms, if the customer requires a fit in house we would fit the engine into the car and ensure all ancillary components needed are sourced, fitted and are in working condition then the vehicle is plugged into our diagnostic equipment and vigorously tested/driven to make sure the vehicle is in working order. Once it is the customer is contacted. We can send the vehicle or the customer can come drive their vehicle out.
